In the fast-paced world of warehouse management, accurately and efficiently tracking inventory is not only beneficial, it's crucial to success. Companies often oscillate between cycle counting and full inventory to maintain accurate stock levels. Both methods offer different benefits and challenges, tailored to different operational needs and business scales. This document delves into the essence of cycle counting and full inventory, illuminating their nuances and helping you decide which strategy might best suit your warehouse management needs.
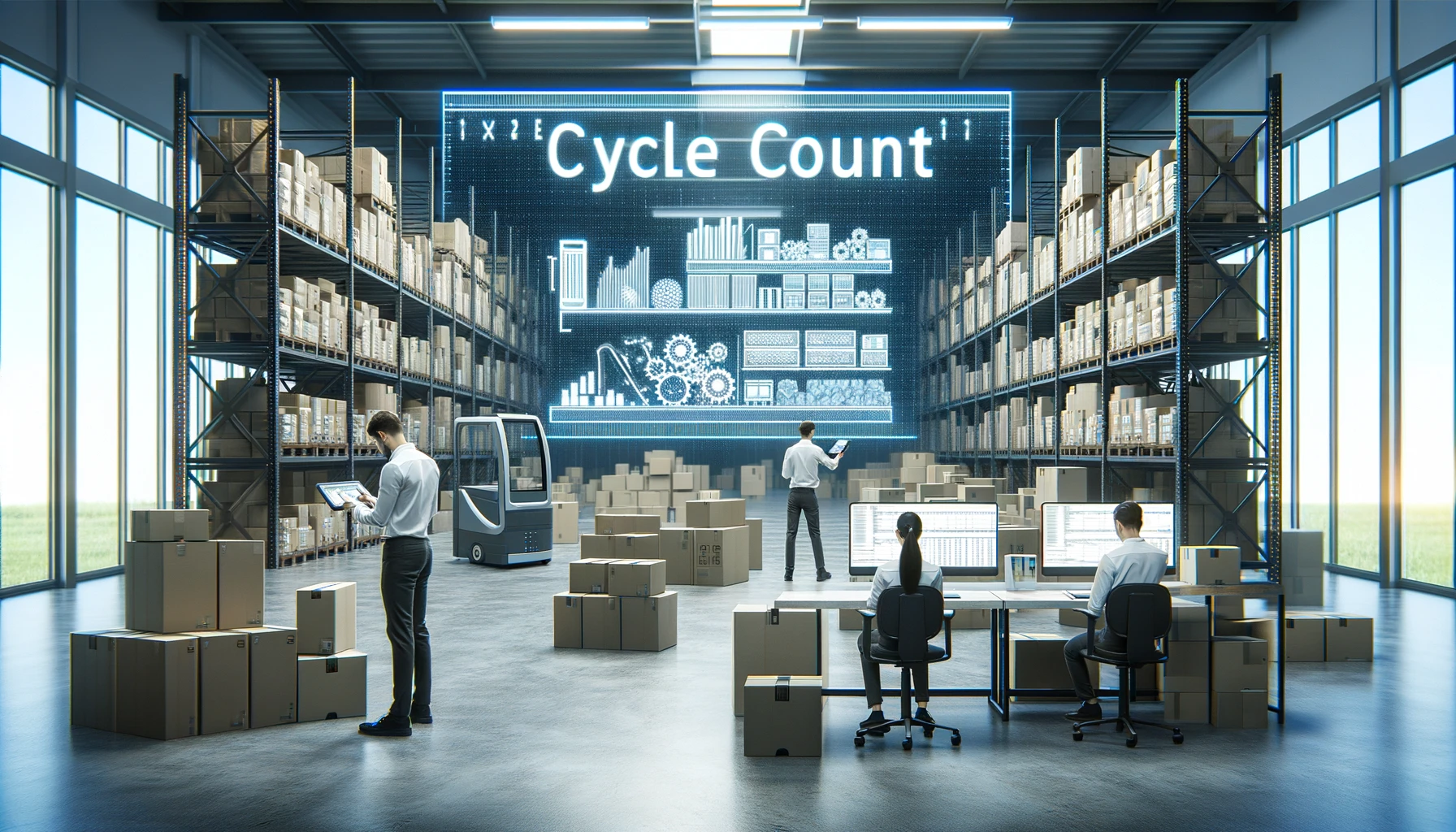
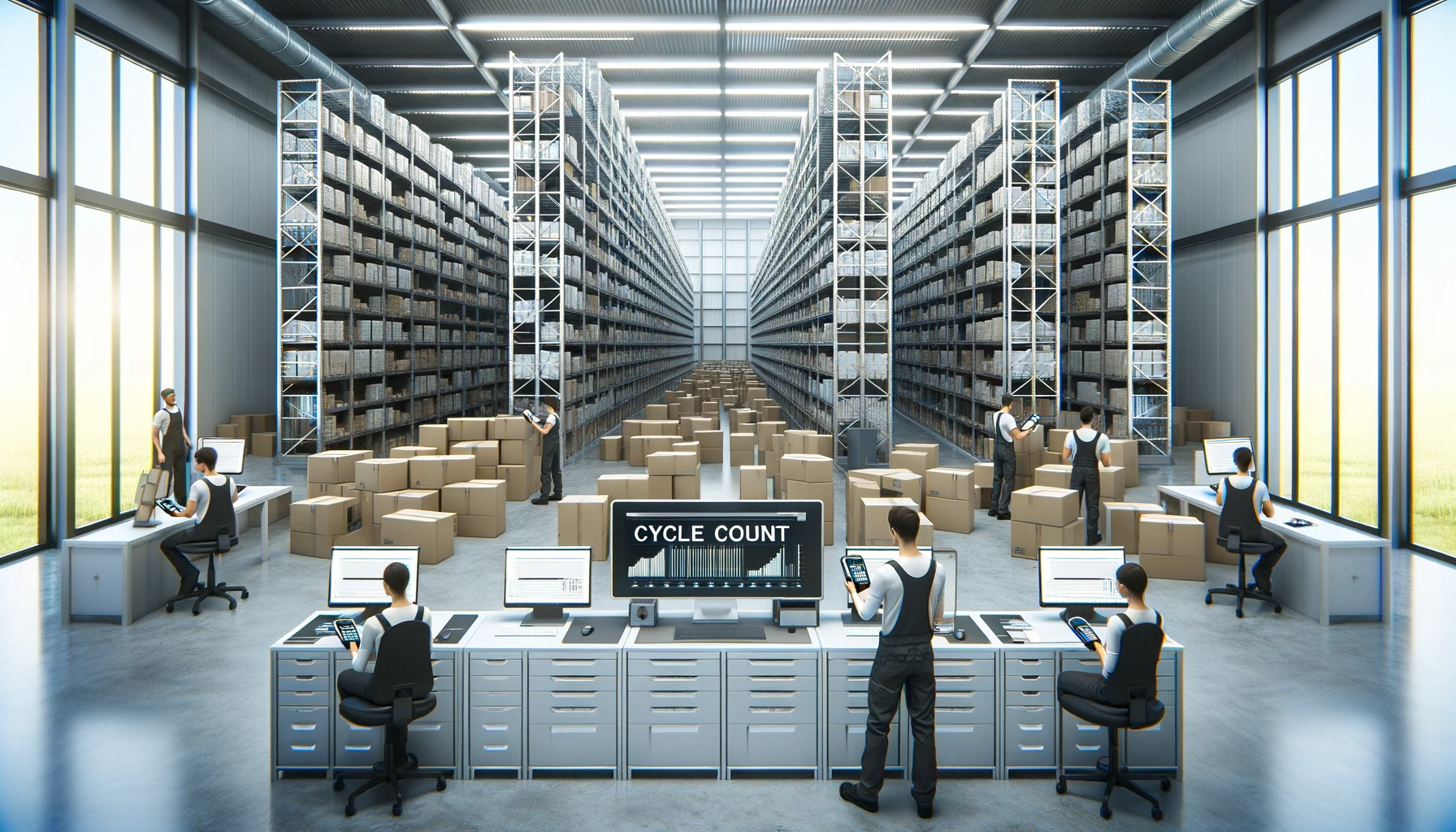
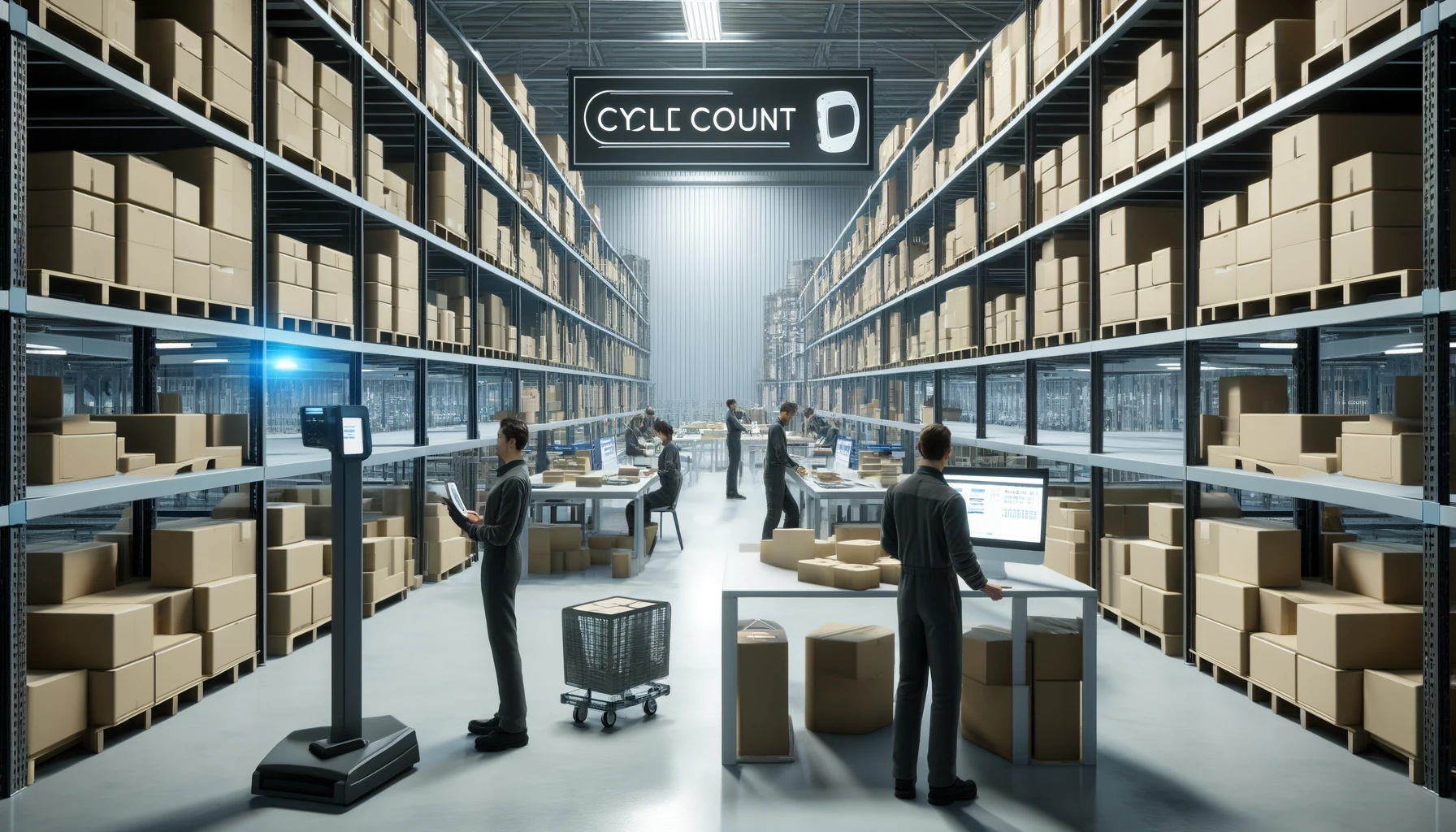
Understanding cycle counting
Cycle counting is an inventory audit procedure where a small subset of the inventory, at specific locations, is counted on a specified day. It is part of an ongoing process to verify the accuracy of inventory data and typically does not disrupt daily operations.
What is cycle counting?
Cycle counting involves regularly scheduled counts of inventory items to ensure stock accuracy and data integrity. Unlike full inventory counts that halt warehouse operations, cycle counting is less disruptive and can be integrated into daily activities without significant downtime.
Benefits of cycle counting
1. Improved accuracy of inventory records: By regularly counting different parts of inventory, discrepancies can be continually identified and corrected, leading to more accurate records.
2. Minimal disruption: Since only portions of inventory are counted at any time, normal warehouse operations can continue without significant disruption.
3. Cost efficiency: Cycle counting can be more cost-effective than full inventories because it requires less overtime and downtime.
Cycle Counting Challenges
1. Requires trained personnel: Effective cycle counting requires that personnel be trained in specific counting techniques and the use of inventory management systems.
2. Time-consuming setup: Implementing a cycle counting program can be time-consuming, involving setting schedules, training staff, and possibly updating or changing inventory software.

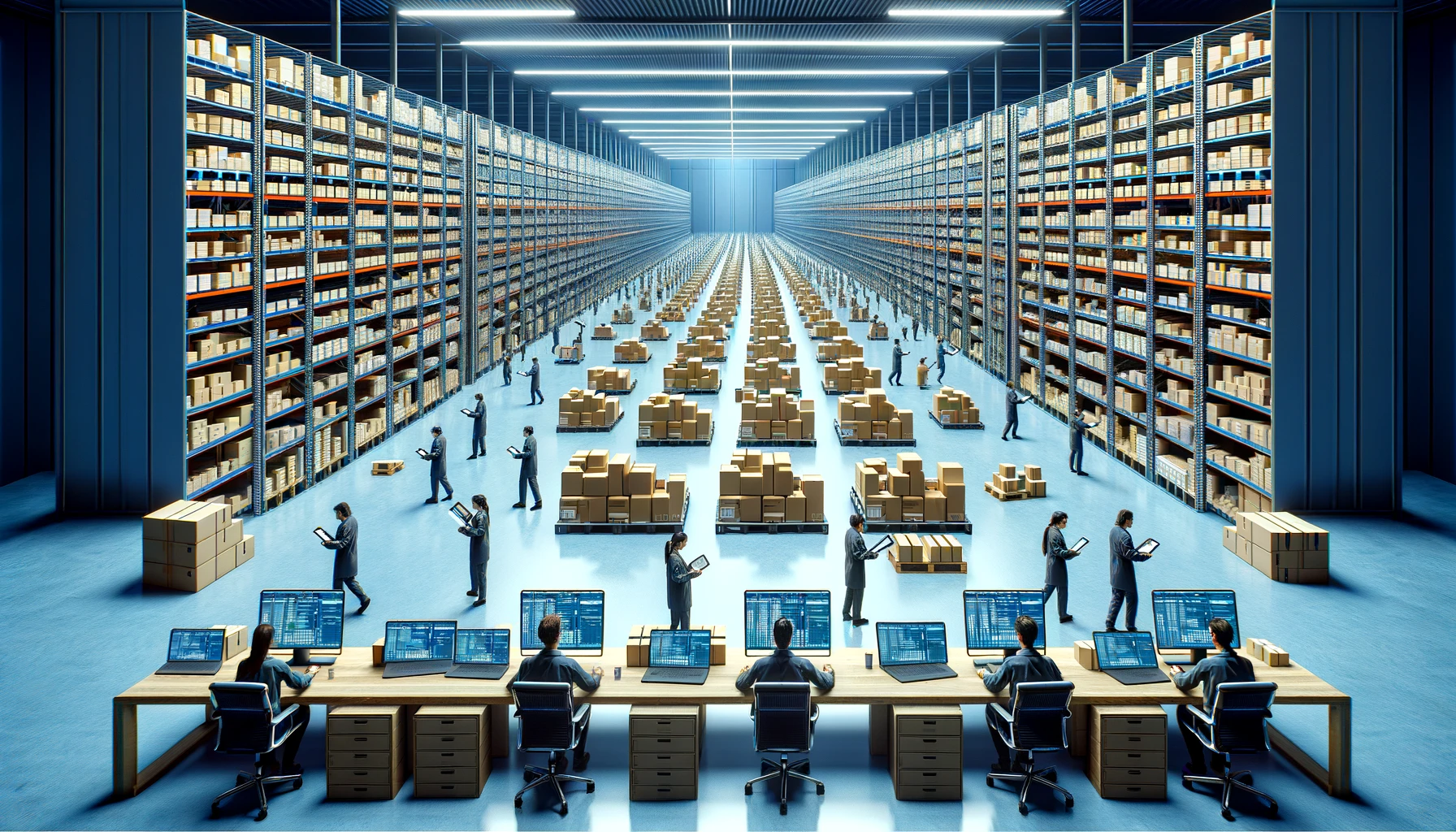

Understanding the complete inventory
A complete inventory, or a physical inventory count, involves counting each item in the warehouse to verify inventory records and account for all stock. This method is thorough, but can be quite disruptive.
What is complete inventory?
Full inventory involves a complete shutdown of warehouse operations to count each item. It provides a snapshot of what is on hand and is usually performed annually as part of the financial audit.
Benefits of full inventory
1. Complete data: A complete inventory count provides a complete snapshot of inventory at a single point in time, allowing for a thorough reconciliation process.
2. Regulatory compliance: For some companies, conducting a complete annual inventory is necessary to comply with accounting or regulatory requirements.
Complete Inventory Challenges
1. Operational disruption: A full inventory count requires stopping regular warehouse operations, which can lead to lost productivity and revenue.
2. Labor intensive and expensive: This method requires more staff and often needs to be performed overtime, increasing operating costs.
Comparison between cycle counting and full inventory
Understanding the key differences between cycle counting and full inventory is crucial to choosing the right approach for your business.
Impact on operations
Cycle Counting: Minimally invasive, it allows the continuity of normal operations with slight interruptions.
Full Inventory: Highly disruptive, requires operational downtime.
Precision and reliability
Cycle Counting: High precision through frequent verifications, although it depends on consistent processes.
Complete Inventory: Provides a complete but infrequent check, risking outdated data between counts.
Cost implications
Cycle Counting: Generally more cost-effective due to reduced downtime and overtime.
Full Inventory: Potentially more expensive due to extensive labor and operational downtime.
When to choose cycle counting over full inventory
Opting for cycle counting might be more beneficial under the following conditions:
- High value inventory where discrepancies could lead to significant financial losses.
- Large warehouses with continuous operations that cannot afford long downtimes.
- Companies seeking to implement lean management practices.
When to go for full inventory
Full inventory may be necessary in scenarios such as:
- Annual financial audit and regulatory compliance.
- Suspected theft or significant discrepancies found during cycle counts.
- Businesses with smaller inventories or those that can afford downtime without significant disruption.
Frequent questions
What are the main advantages of cycle counting over full inventory?
How often should cycle counting be performed?
Is full inventory more accurate than cycle counting?
What type of technology is best to support cycle counting practices?
Can cycle counting replace full inventory for financial audit purposes?