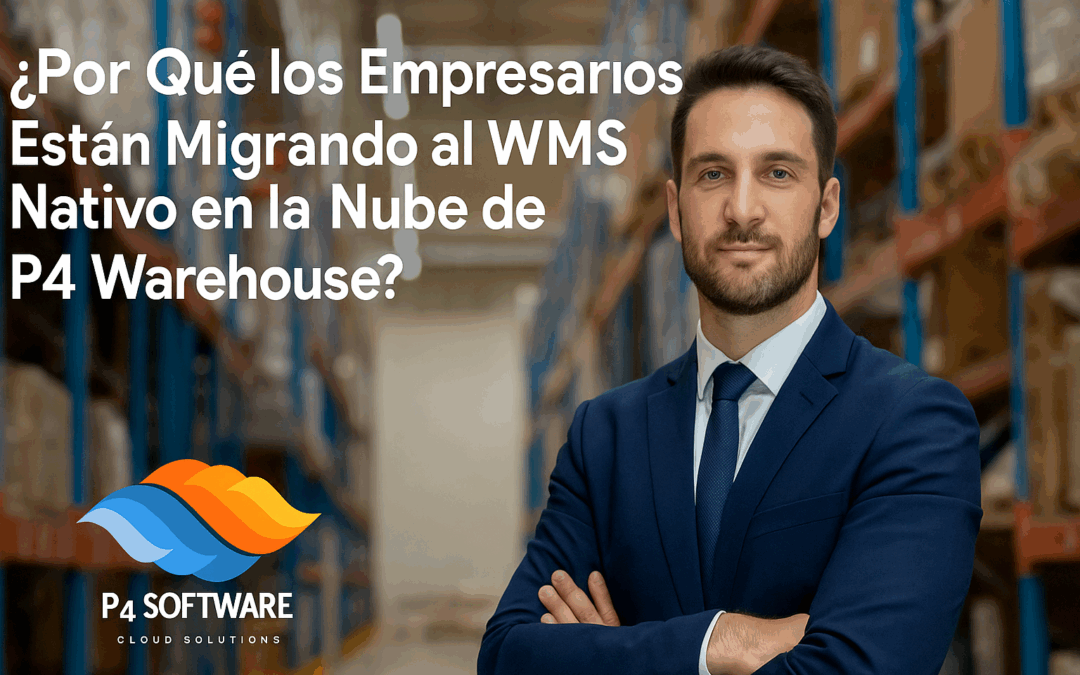
Why Are Businesses Migrating to P4 Warehouse's Cloud-Native WMS?
Your WMS should generate profits — not be a bottleneck
You already have a solid operation: good equipment, quality products, and ever-growing demand. But there's one thing that constantly holds you back: the warehouse.
Shipping delays. Out-of-stock products. Expired inventory. Customer complaints.
And in most cases, the root problem is your warehouse management system.
Legacy WMS Systems: Why Don't They Work Anymore?
Many traditional WMSs were designed before cloud computing, mobile scanners, or real-time integration with an ERP. They never evolved—and that's costing you more than you think.
The reasons:
- Rigid and obsolete logic
They use fixed rules that don't adapt to what's happening in real time. The inventory may be there, but the system can't find it in time. -
False integration
Many claim to integrate with SAP or other ERPs, but in reality, they use batch uploads, legacy connectors, or manual processes. This disrupts your complete order-to-cash cycle. -
Hidden costs
They require their own servers, specialized technical staff, and hours of consulting for each change. What seemed like a one-time purchase becomes an ongoing expense. -
Designed for technicians, not business people
If you need a scheduler to know what you have in stock or the status of an order, you've already lost agility. Your system should empower you, not limit you. -
Reactive, not preventive, systems
They don't alert you about expiring products, packaging errors, or picking delays until the damage is already done. And that translates into lost customers and lost profitability.
The Solution: P4 Warehouse, a Cloud-Native WMS
P4 Warehouse eliminates complexity and replaces it with speed, accuracy, and intelligence.
It is designed to work as your business needs:
-
Real-time traceability, from platform to platform
-
Full integration with SAP and modern ERPs
-
Smart allocation with due date management and FIFO logic
-
Mobile scanning with live inventory display
-
Automatic generation of labels, shipping guides, packing slips and audits
-
Capture digital signatures and upload shipping photos
-
Multi-client and multi-warehouse support from day one
And since it's completely cloud-native:
It requires no servers, technical equipment, or legacy infrastructure.
Clear Benefits for Business Owners
- Fewer errors and faster shipping mean greater customer loyalty.
- Better inventory visibility enables smarter purchasing and less shrink.
- Lower cost per order translates into higher margins.
- Automated compliance reduces legal and operational risks.
- Scalable architecture ready to grow without interruptions.
Real Companies Are Already Using It
P4 Warehouse operates in Panama, Ecuador, the United States, and Canada, handling high-volume products, pharmaceuticals, frozen foods, and more.
With the launch of P4 Pharmaceutical Warehouse 2024 and the expansion to Europe in 2025, the future of logistics is already a reality.
Regain Control of Your Supply Chain
You shouldn't be chasing answers inside the warehouse. You should have visibility, accuracy, and confidence from the system.
Visit: https://p4.software
Schedule a live demo and discover how P4 Warehouse can take your operation to the next level.